The examinations shall ensure that:
(a) The elements are inspected externally for pitting, corrosion, abrasions, dents, distortions,
defects in welds or any other conditions, including leakage, that might render the MEGC
unsafe for carriage;
(b) The piping, valves, and gaskets are inspected for corroded areas, defects, and other conditions,
including leakage, that might render the MEGC unsafe for filling, discharge or carriage;
(c) Missing or loose bolts or nuts on any flanged connection or blank flange are replaced or
tightened;
(d) All emergency devices and valves are free from corrosion, distortion and any damage or defect
that could prevent their normal operation. Remote closure devices and self-closing stop-valves
shall be operated to demonstrate proper operation;
(e) Required marks on the MEGC are legible and in accordance with the applicable requirements;
and
(f) The framework, the supports and the arrangements for lifting the MEGC are in satisfactory
condition.
The inspections and tests in 6.7.5.12.1, 6.7.5.12.3, 6.7.5.12.4 and 6.7.5.12.5 shall be performed or
witnessed by a body authorized by the competent authority. When the pressure test is a part of the
inspection and test, the test pressure shall be the one indicated on the data plate of the MEGC. While
under pressure, the MEGC shall be inspected for any leaks in the elements, piping or equipment.
When evidence of any unsafe condition is discovered, the MEGC shall not be returned to service until
it has been corrected and the applicable tests and verifications are passed.
Marking
Every MEGC shall be fitted with a corrosion resistant metal plate permanently attached to the MEGC
in a conspicuous place readily accessible for inspection. The metal plate shall not be affixed to the
elements. The elements shall be marked in accordance with Chapter 6.2. As a minimum, at least the
following information shall be marked on the plate by stamping or by any other similar method:
(a) Owner information
(i) Owner’s registration number;
(b) Manufacturing information
(i) Country of manufacture;
(ii) Year of manufacture;
(iii) Manufacturer’s name or mark;
(iv) Manufacturer’s serial number;
(c) Approval information
(i) The United Nations packaging symbol

;
This symbol shall not be used for any purpose other than certifying that a packaging, a
flexible bulk container, a portable tank or a MEGC complies with the relevant
requirements in Chapter 6.1, 6.2, 6.3, 6.5, 6.6, 6.7 or 6.11;
(ii) Approval country;
(iii) Authorized body for the design approval;
(iv) Design approval number;
(v) Letters ‘AA’, if the design was approved under alternative arrangements (see 6.7.1.2);
(d) Pressures
(i) Test pressure (in bar gauge)3;
(ii) Initial pressure test date (month and year);
(iii) Identification mark of the initial pressure test witness;
(e) Temperatures
(i) Design temperature range (in °C)3;
(f) Elements / Capacity
(i) Number of elements;
(ii) Total water capacity (in litres)3;
(g) Periodic inspections and tests
(i) Type of the most recent periodic test (5-year or exceptional);
(ii) Date of the most recent periodic test (month and year);
(iii) Identification mark of the authorized body who performed or witnessed the most recent
test.
3 The unit used shall be indicated.
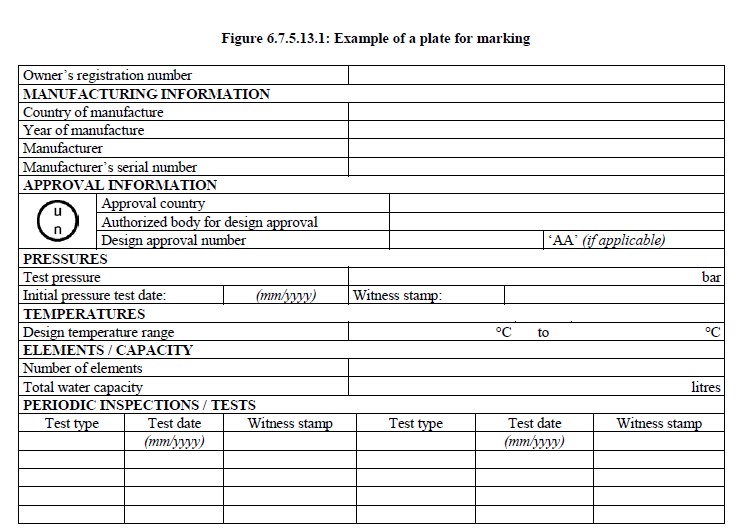
The following information shall be durably marked on a metal plate firmly secured to the MEGC:
Name of the operator
Maximum permissible load mass ________ kg
Working pressure at 15°C: ________ bar gauge
Maximum permissible gross mass (MPGM) __________ kg
Unladen (tare) mass _________ kg
REQUIREMENTS FOR THE CONSTRUCTION, EQUIPMENT, TYPE APPROVAL, INSPECTIONS AND TESTS, AND MARKING OF FIXED TANKS (TANK-VEHICLES), DEMOUNTABLE TANKS AND TANK-CONTAINERS AND TANK SWAP BODIES, WITH SHELLS MADE OF METALLIC MATERIALS, AND BATTERY-VEHICLES AND MULTIPLE ELEMENT GAS CONTAINERS (MEGCs)
NOTE 1: For portable tanks and UN multiple-element gas containers (MEGCs) see Chapter 6.7, for fibrereinforced
plastics tanks see Chapter 6.9, for vacuum operated waste tanks see Chapter 6.10.
NOTE 2: For fixed tanks (tank-vehicles) and demountable tanks with additive devices, see special provision 664
of Chapter 3.3.
Scope
The requirements across the whole width of the page apply both to fixed tanks (tank-vehicles), to
demountable tanks and battery-vehicles, and to tank-containers, tank swap bodies and MEGCs. Those
contained in a single column apply only:
- to fixed tanks (tank-vehicles), to demountable tanks and battery-vehicles (left hand column);
- to tank-containers, tank swap bodies and MEGCs (right hand column).
These requirements shall apply to:
fixed tanks (tank-vehicles), demountable tanks
and battery-vehicles
|
tank-containers, tank swap bodies and MEGCs |
used for the carriage of gaseous, liquid, powdery or granular substances.
Section 6.8.2 sets out the requirements applicable to fixed tanks (tank-vehicles), to demountable tanks,
tank-containers, tank swap bodies intended for the carriage of substances of all classes and batteryvehicles
and MEGCs for gases of Class 2. Sections 6.8.3 to 6.8.5 contain special requirements
supplementing or modifying the requirements of section 6.8.2.
For provisions concerning use of these tanks, see Chapter 4.3.
Requirements applicable to all classes
Construction
Basic principles
Shells, their attachments and their service and structural equipment shall be designed to withstand
without loss of contents (other than quantities of gas escaping through any degassing vents):
- static and dynamic stresses in normal conditions of carriage as defined in 6.8.2.1.2 and
6.8.2.1.13;
- prescribed minimum stresses as defined in 6.8.2.1.15.
Previous Matter
Next Matter